Cadmium Applications
Cadmium coatings
Cadmium Applications
Key applications of cadmium coatings
Benefits in brief
Primary Benefits
- Excellent corrosion resistance
- Good bondability to adhesives
- High lubricity (friction reduction)
- Exceptional electrical conductivity
- Easy solderability
Secondary Benefits
- Cathodic protection of steel
- Galvanic compatibility with aluminium
- Freedom from stick-slip when torquing
- Good malleability
- Resistance to hydrogen embrittlement
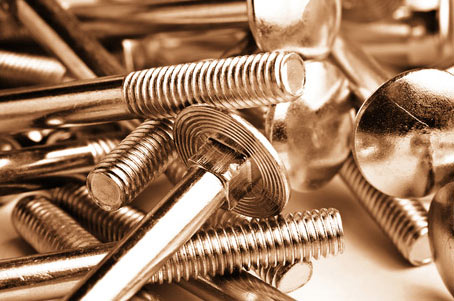
Electroplating
Mechanical plating
Thermal vapour/vacuum deposition and ion deposition
Cadmium Applications
Primary benefits in depth
Excellent corrosion resistance
Cadmium plating serves as a sacrificial coating, meaning that it is preferentially corroded when the coating is damaged and small areas of the substrate are exposed. The cadmium coating is applied in thin layers and can itself be covered with a chromate conversion coating. This second conversion coating enhances the corrosion resistance of cadmium plating while giving it a characteristic golden-yellow, olive drab or bluish clear colour. Cadmium plating is more resistant than zinc plating in industrial settings and salt-water environments, and offers superior lubricity and malleability compared to nickel.
Good bondability to adhesives
When an object is plated with cadmium, the surface of the object becomes more bondable to adhesives. This makes cadmium plating an outstanding base for paint.
- ship engine
High lubricity
The exceptional lubricity (friction reduction) of cadmium plating is extremely useful when components that will be repeatedly disassembled and reassembled must be plated. It is also beneficial in applications where different metal surfaces are constantly moving, rotating, or touching one another.
Excellent electrical conductivity and easy solderability
Cadmium plating has low electrical resistance and exceptional conductivity, favourable compatibility with aluminium, and superior solderability. Cadmium is therefore an excellent choice of material to plate metal products.